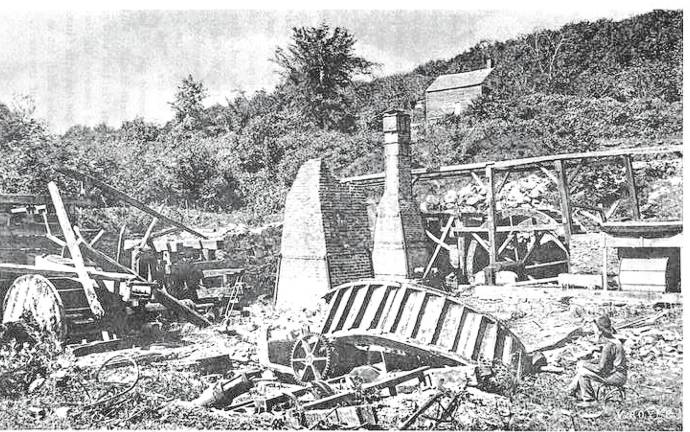
With sinkholes populating Route 80, our region’s mining history has become of great interest.
We recently spoke of the mines near Jefferson and Rockaway. Some were deep and some shallow, and their location was of high importance.
In addition to mining, the ore had to be processed. Rock removed from the mine included valuable iron, but the iron had to be separated out.
When the mines closed in the 1890s, they left a legacy of sinkholes that have occurred during the years. Believe it or not, some piles of unprocessed iron ore are still around, and a magnet will stick to the rock.
During hundreds of years, the way to separate the iron has evolved. At one point in time in America, namely the 1840s through the 1880s in northern New Jersey, the ore would be placed on a fire and the iron melted out. The high heat, more 2,000 degrees Fahrenheit, would require, in addition to a strong charcoal fire, additional air to bring it up to the needed temperature.
In those days, a bellows would be used. Wood and leather would make for a pocket that could suck in air through a one-way valve, then be pressed to push the air out to the fire.
To do this, waterpower was usually the prime source of “fuel.” On a stream or river, a waterwheel would be driven by the water coming by. The shaft that spun would be connected by pillow blocks along the way to spokes or a lever that would be raised and lowered as the shaft spun. This would open and close the bellows.
The iron would melt and run out of the furnace to make a puddle. This would be a bloom. Small operations like this, along modest streams, were called a bloomery.
To consolidate and purify iron, it would be pounded by a hammer. This was on a lever. On the beam was a heavy piece of already produced iron strapped to the lever. The lever was forced up and dropped down by the rotating shaft of a waterwheel.
An expression for this industry, along with the furnace, would be generally called a forge. This is what we will talk about today with the Windham Forge.
To be more thorough, an industry also might have a place to make parts from the iron. This operation might be called a foundry, alongside the forge. An example of this was the Franklin Furnace.
Windham Forge was along the Pequannock River in Hardyston Township in today’s Stockholm (an older name was Snufftown).
Windham Forge was probably built by Matthias Winans as New Forge or Wingdam about 1770. It was owned by John O. Ford about 1790, changed hands to a Kinkaid, then to Riggs. It operated during much of the 1800s.
This was one of some 30 water-powered industries along the river. Windham was conveniently located on the Paterson-Hamburg Turnpike for easy transport. It is said that leather was tanned in Snufftown area, transported by oxen down to the Dover area, where iron ore from the mines near today’s Route 80, along with ore from Ogden’s (Edison’s) and Ringwood. Windham was a relatively large forge.
This photo was taken in the late 1800s after the forge closed and became abandoned. Stone remains still exist and can be seen from Old Route 23 along the boundary of Sussex County.
Much more can be said of the Windham Forge and of how a forge operates. Some components of a forge are on display on Route 23 North a few miles east of Windham Forge on a turnout.
The workings of a forge are a topic for another time. Hopefully, we can see the depth and breadth of the iron mining heritage that we have here in our region.
A source of much of this article is the North Jersey Highlander and the associated historical society. I cannot emphasize enough the rich library of material that they have. I encourage you to contact Ralph Colfax at 0kimberly0colfax0@gmail.com
Bill Truran, Sussex County’s historian, may be contacted at billt1425@gmail.com